ALCAN SINGEN GMBH
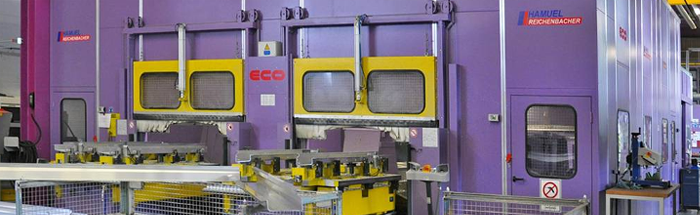
Alcan Singen GmbH is an aluminium manufacturing plant with about 1,800 employees. With its various production activities Alcan Singen GmbH represents one of the largest sites within Constellium. Today Alcan Singen plant develops, manufactures and distributes specialty sheets and coils, extruded products, automotive components and systems in aluminium lightwheight construction. By constant development and innovation, aluminium products from Singen enjoy an excellent reputation worldwide. The plant with its diversity belongs to the leading suppliers for many years in the industry, building, automotive, transportation, mechanical and electrical engineering markets.
Two identical Reichenbacher CNC machining centres, type “ECO-1520-C” are at ALCAN Singen in Neckarsulm in operation. These two ECOs are state-of-the-art two-gantry-machines with large motor assembly on four aggregate slides. Thus ALCAN is in a position to fulfil the rose requirements of their customers (Jaguar, Daimler, Audi etc.) even more effectively and with high quality. Each machining centre is equipped with two fixed and low vibration three-post-gantries and two separately moveable machining tables. Several aggregates are installed at the front and back side of the gantries. A special feature is that the aggregates are in a position to operate on the left as well as on the right machining table. Due to this configuration loading works and tool changes can be carried out with no downtimes.
- Machine table: steel plate with an appropriate interface for placing existing devices; dimensions 2,000 x 1,500mm
- Available working space for each machine table: 1x 1,600 x 2,000 x 450mm, 2x 800 x 2,000 x 450mm, 4x 400 x 2,000 x 450mm
- Between the tables a centre partition is installed; the machine is completely enclosed with a sound insulating cabin with ceiling ele-ment
- Feed speed: X = 80 m/min; Y = 80 m/min; Z = 20 m/min
- Aggregate equipment gantry 1 front side, aggregate group 1 and 2: each 4x routing aggregate 1.8 kW, max. 18,000 1/min, tool fixture HSK-C40
- Aggregate equipment gantry 1 rear side, aggregate group 1 and 2: each 2x horizontal routing aggregate 3 kW, max. 12,000 1/min, collet chuck
- Aggregate equipment gantry 2 front and rear side: each 1x fork head 24 kW, max. 21,000 1/min, tool fixture HSK-B80 with blast nozzle and minimum quantity lubrication for operating of aluminium
- each 1x disc tool changer for 12 tools, hollow cone shank HSK-E63
- each 1x pick-up place for a saw blade with max Ø 600mm
- Cooling and lubrication unit which blows a mixture of oil and air to the cutting edge. Altogether 18 separately controllable nozzles.
- Siemens control, type Sinumerik 840D sl in moveable control panel with 17" TFT-monitor including manual control unit, tele-service and Siemens Safety Integrated
The first gantry has 2 x 4 vertical routing spindles (front side) and 2 x 2 horizontal routing aggregates (back side). The second gantry has two 5-axis routing aggregates (one at the back and one at the front side). The tool changers move with the aggregate slide, thus no stroke for tool changing is necessary.
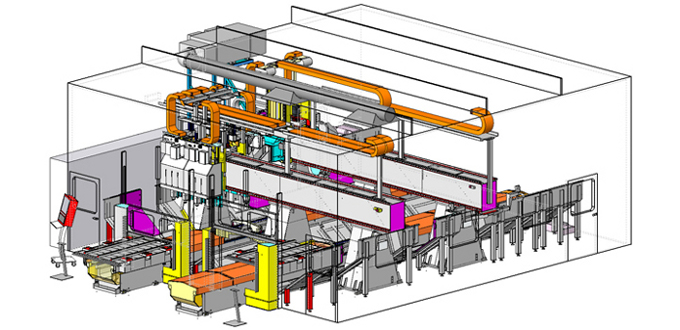
During operation the tables are inside the protection cabin. For loading the tables run out and are accessible from the front and both outer sides. The openings in the cabin front are carried out as pneumatic lifting gates with safety windows.
Due to the 2-channel control different components can be operated on both machining tables at the same time. As there are no geometrical restrictions due to the special aggregate configuration, all aggregates can be used when programming the components and can be freely allocated to the individual production steps.
