RENGGLI AG
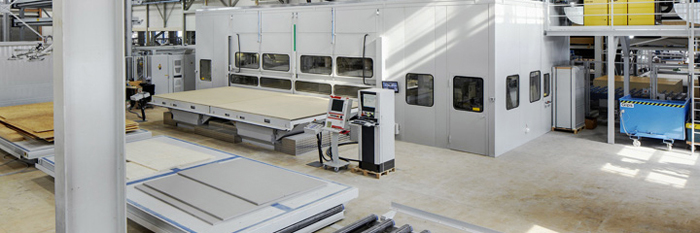
The Swiss company RENGGLI AG based in Schötz near Lucerne manufactures innovative wooden buildings. All Renggli building projects combine high levels of comfort with energy efficiency. Minimising energy consumption is a key element in Renggli’s commitment to sustainability and environmental protection which they call “Minergy standard”. Innovative thinking was also behind the company’s new factory in Schötz. Efficiencies were introduced into the manufacturing process, capacity was designed to accommodate growth and shorter lead times were combined with quality improvements. For this reason the owner, Max Renggli, invested in high-tech equipment. At the heart of the new manufacturing facility is a panel machining centre – representing the state of the art in terms of flexibility, quality and speed – an ECO 3533 B-Sprint made by Reichenbacher Hamuel.
As well as supplying the machining centre as centrepiece of the innovative process, Reichenbacher also worked with Renggli in the design and construction of the entire production unit. This ensured that everything interfaced smoothly. The robot cares for quick supply of all machining stations. It manages a total of 125 storage positions covering an area of 2,670 square metres and enables unmanned operation of the plant.
- Machine dimensions (floor space) approx 24,000 x 14,000mm
- 2 machine tables, divided into 16 vacuum areas, individually controllable, nesting table to be covered with a stainless steel plate for a plane table with double circuit pods
- Working area each table 3,500 x 3,300mm, coupled 7,000 x 3,300mm
- 5 pneumatically sinkable stops each machine table
- Feed rate: X = 90 m/min; Y = 60 m/min; Z = 40 m/min
- Axis strokes: X1/2 = 8,000mm; Y1/2 = 10,100mm; Z1 = 900mm; Z2 = 550mm
- 5-axis working spindle, 24 kW performance, HSK-F63, revolutions 500 - 24.000rpm
- SIVIB for monitoring the admissible tool unbalance
- Drilling unit with 40 drills BDE3 with 8x 1.7 kW performance, drive direction right
- Printing and labelling system at the Z-axis in front of the drilling head
- Automatic chain magazine for 80 tools; the working head respectively the routing spindle is supplied with the pre-selected tool by double-gripper module
- Measuring pin for the vertical measuring of part positions in the X/Y-plane; tracing head to be taken from the tool magazine
- 2x pick-up tool places for sawing tools up to a diameter of 740mm
- Chip removal package with 2 pneumatically activated units for pushing off the waste parts for cleaning the table and 2 additional brushes for cleaning the parts
- 2 rotary screw vacuum pumps with 942 m³/h suction capacity each, make Kaeser
- Machine with sheet steel enclosure, two pneumatic lift gates in the front side of the enclosure
- Siemens control type Sinumerik 840D sl in moveable control panel with 17" TFT-monitor, including tele-diagnostic, multi-channel technique
- Wireless hand control device, software NC-HOPS V5.0
A delivery passage, controlled via an automatic storage and retrieval system, supplies the high-rack store directly from the delivery vehicle. Both raw materials and purchased components are stored here ready for further processing. There is also an option to operate the whole system in partially automatic mode by a separate storage and retrieval area and by manual raw material and finished part positions. The Reichenbacher machining centre is automatically fed and unloaded by robot.
Overview of the entire unit and its peripheral devices
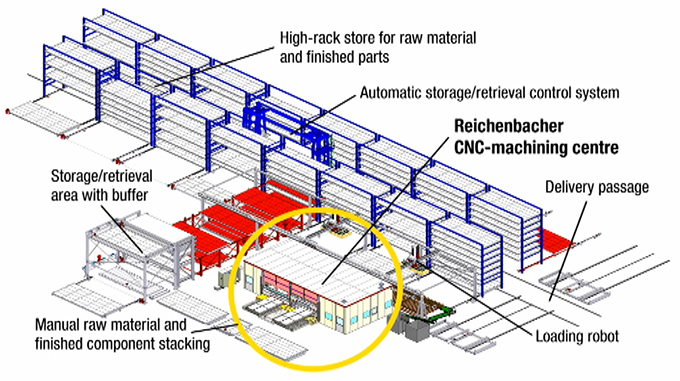
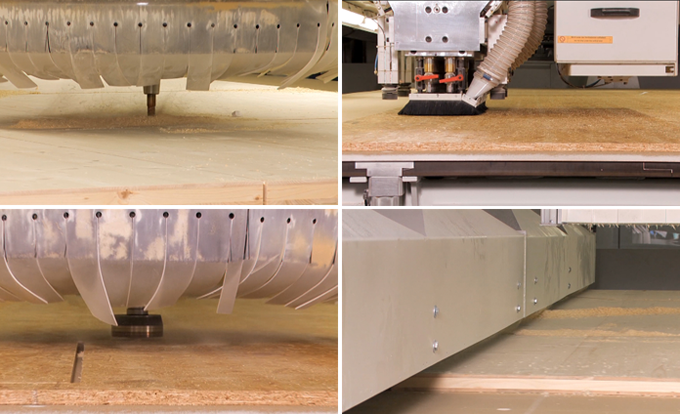